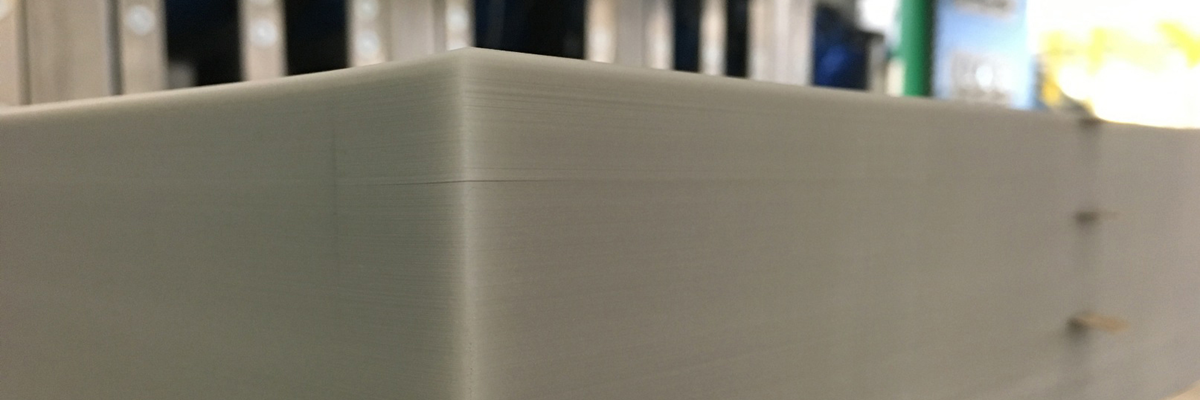
High Speed Sheeting for Plastic Film is now possible
With its revolutionary air stream sheet transportation systems, the RQS-V Questec Film Sheeter is a proven solution to converters of light-weight plastic film and paper
Manufacturers and converters, wishing to cut delicate materials, typically struggle with achieving mark-free results on security documents, solar panels, and materials used in the automotive and aviation industries. To prevent ultra-thin, delicate and electrostatically charged single web films or light papers from crinkling and soiling, the mechanical handling is the key solution.
The RQS-V Questec Sheeter is BW Papersystems’ approach to eliminate this issue: “The RQS-V variable size Sheeter is unique. After years of development, the experienced Questec team has systematically overcome these problems. Questec engineers
developed a new way to transport sheets. The Air Stream system moves sheets without tapes, rollers or belts. This gives huge benefits for normal and very light substrates. Because there is no mechanical contact with the substrate, surface marking
is eliminated. This is particularly important for hi-tech coated films or high graphics printed webs,”explains Steve Brimble, Questec Product Leader & VP Strategic Accounts at BW Papersystems.
Thin films and coated paper cause
problems for the processing industry due to the electrostatic charge. Uncontrolled discharges can significantly disturb manufacturing processes. With a newly developed Questec system, that is comparable to a vehicle’s ABS system, the problem
of electrostatic charging is neutralized. Mastering this interference factor leads to increased productivity.
Faster and safer: The air transport system for extremely light films and papers
Cutting thin films or papers
quickly and with stepless variable lengths, to accelerate production processes, is BW Papersystems’ strength. “By adding this leading technology for cross cutting ultra-thin, delicate and electrostatically charged single web films or light
papers to BW Papersystems’ portfolio, our Questec team has not improved on an existing concept, we have invented an entirely new concept.”, says Dirk Luenenschloss, Questec Engineering Leader at BW Papersystems. The sheets are effectively
pulled by air – instead of pushed by belts – through the process, without any mechanical contact. This allows mark free results at a high speed for sensible products, such as plastic film, lightweight and specialty papers.
The
conventional sheet transportation technique of a line transport system leaves a long gap of access or guidance of the film or paper sheet. This causes disturbances and therefore production stoppages. Whereas BW Papersystems’ revolutionary “Air
Stream” sheet transportation technique of the Questec Sheeter offers a nearly gapless transfer and takeover of the material to be cut, leading to a steady and safe production. The material is under positive control from the section before the
cross cut knife until the sheet is transported to the end of the stack. No other sheeter eliminates the need to “push” the sheets during delivery. Questec technology provides full control of the sheet until it is placed into the final
stacked position. This technology provides precision cut and stacked sheets without the need for wasteful guillotine trimming.
The Questec Film Sheeter
When transporting and cutting single-layer papers, starting from
30 g/m2 and plastic film starting from 80 μm, at a cut-off length of 400 mm to 1.050 mm, and at a leading production speed up to 400 m/min (1,300 ft/min) or even 600 m/min (1,960 ft/min.)1, the Questec Sheeter offers highly competitive technology.
For special applications, their sheet delivery system allows far longer sheet lengths than normal to be delivered. It’s available in 850mm and 1350mm widths.
Starting from the roll, ease of operation, efficiency and waste reduction
are key design features. A shaftless self-loading unwind with tension maintained by brakes or motors is standard. Decurling and edge guiding functions are provided between the unwind and the sheeter entry. Options such as cut to print register, corona
treatment, perforating or coating are available as options.
As the web enters the Sheeter, the optional side trimming and center slitting is available. Trims can be rewound or removed via a blower. A segmented nip roll system pulls the web into the sheeter and a system keeps the web under control after the nip point up to the cross cut point.
The semi synchronized cross cut knife produces the highest quality of accuracy, cut quality and squareness without causing air turbulence. The sheets are then held and conveyed under positive control until they arrive at their final location on the stack.
Stacking quality is maintained for front and side jogging. Finished sheets have commercial level cut quality, accuracy and stack quality eliminating the need for guillotine trimming.
An advanced drives and controls package ensures that
job specific adjustments are easily set and stored for future use. Remote diagnostics are standard allowing BW Papersystems’ global support team to provide the fastest possible intervention.
Significant results
Having successfully installed and tested the plastic film folio sheeters at the industry’s major key players across the globe, who convert materials including polycarbonate, polyester or even solar panels, Frederic Duquenne, Questec Global Sales Leader at BW Papersystems, is convinced: “Production with our film folio sheeters led to significant results: better sheet accuracy in multi-pockets applications; removed the guillotine process; better sheet handling; and also higher speeds. However, we haven't tested the limits of the Questec sheeter in all its possibilities so far!”
Transferring paper industry expertise to the plastic and film industries
Due to its variability, the Questec Sheeter has a lot of potential for various industries. Patrick Walczak, Senior Vice President Sales at BW Papersystems, looks ahead optimistically and confidently. “Being able to transfer our cutting-edge technology to the film and plastics industry, opens up a new window. Thus, we analyzed the market and came to the conclusion, that high quality standards, most efficient production methods and innovative technology with tangible added-value for the industry are an overlapping need between industries. BW Papersystems can provide a solution also for the plastic industry, which is unique. To get an even better feeling of how our new technology can benefit operations, we are going to attend the K 2019 exhibition this coming October. We look forward to introduce our new technology there, while collecting new information and receiving valuable feedback.”
TOP FACTS AT A GLANCE:
Benefits:
• High-speed sheeting for film and paper
• Converting of lightweight materials with sensitive surface characteristics, eg. cut-to-register or beer labels
• Inline applications for Web Offset, Gravure or Flexographic presses
• Highly accurate cutting tolerance of ±
0,15 mm
• Mark free results
• less than 50% of the length of a conventional high speed sheeter
• Less adjustments points and so faster set up times
• Set up memory to replicate the perfect running conditions
for each job
• Virtually maintenance free
Applications:
• For plastic film manufacturers and converters
• For light weight paper manufacturers and converters
Technical Data | |||||||||||
RQS-85 | RQS-135 | ||||||||||
Max. web width | 850 mm (33.46”) | 1.350 mm (53.14”) | |||||||||
Min. web width | 400 mm (15.74”) | 400 mm (15.74”) | |||||||||
Sheet length | min. 400 mm / 15.74” max. 1.050 mm / 41.33” | ||||||||||
Paper / board grammage | min. 30 g/m2 max. 300 g/m2 | ||||||||||
Film thickness | min. 80 μm max. 300 μm | ||||||||||
Max. Mechanical speed | 400 m/min. / 1,300 ft/min. optional: 600 m/min. / 1,960 ft/min.2 | ||||||||||
Cut accuracy | +/- 0.15 mm / 0.006” | ||||||||||
Pallet height | 1500 mm | ||||||||||
Number of webs | 1 | ||||||||||
Number of pockets | 2 | ||||||||||
Substrate | Film, paper, board, beer labels, spe-cialties papers | ||||||||||
Options available | Cut-to-register, inline coating, inline embossing, non-stop pallet change, remote diagnosis, sample gate |
1, 2 dependent upon material characteristics
Find Your Machine
BW Papersystems offers a wide selection of paper industry equipment with industry-leading technology.
Learn more about the BW Papersystems equipment and products offered.