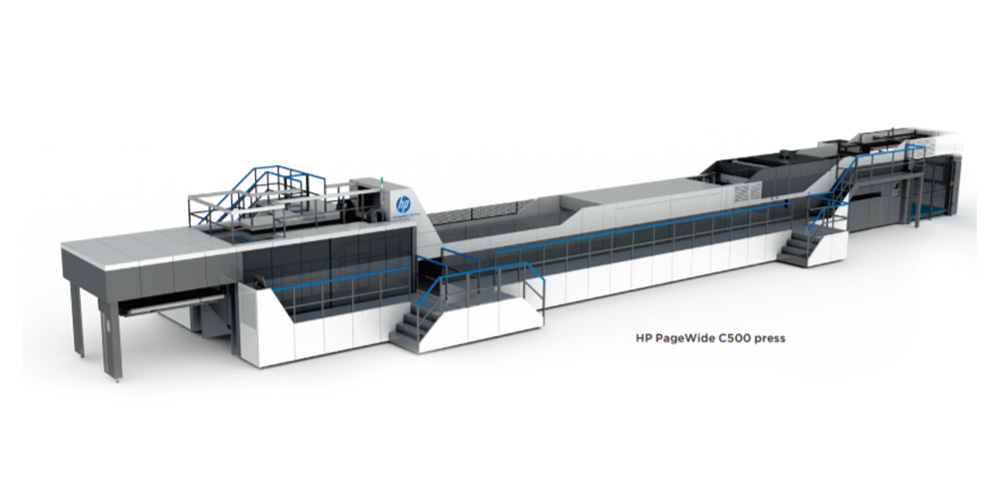
NEW DIGITAL COLLABORATION
HP and BW Papersystems are combining their respective proficiencies in digital printing and analog printing and converting to drive cost out of the process of making graphic corrugated packaging. They are proposing a near-line solution that integrates an HP PageWide C500 single pass digital press with a BW Papersystems rotary diecutter. The line will enable corrugated packaging providers to deliver high-speed digital capabilities, ideal for displays, personalization, e-commerce, and the shortest runs with the lowest converting costs, according to Ted Samotis, Director of Go-To-Market for HP PageWide Industrial Corrugated.
“Our intent is to deliver on a lowcost value stream that can compete effectively in markets such as litho lam, litho label and smaller quantity postprint,” he says. Examples of suitable applications include pizza boxes, beer cases and pet food trays, all of which represent lucrative markets for corrugated converters but require several processes to manufacture. For instance, pet food trays often consist of three or four different sizes for several hundred SKUs of product. In the traditional model, labels are printed on an offset press and then laminated and diecut.
“With these market verticals there is a misalignment in the market need and the manufacturing and the supply chain to deliver that market need effectively,” he says. “Our job is to develop solutions that can meet the market and supply chain needs of the brands and do it in a way that moves closer to make to order.”
The current supply chain trends of make to order, closer to point of use and more distributed manufacturing are closely aligned with the value of digital printing, according to Samotis. “The number of brands converting to a digital supply chain is growing, and the capacity is increasing in the corrugated industry, but more work is necessary to drive down the converter’s cost to make a box,” he says.
It is estimated that less than 5% of corrugated plants have digital printing capabilities. “In other printing markets inkjet has been around a long time but it has failed to capture a significant share of the volume in corrugated because it’s too expensive versus the analog alternative,” he says. “The difference between commercial printing and graphic corrugated packaging is that once an item is manufactured in a digital supply chain, it rarely goes back to an analog supply chain.”
Samotis acknowledges that the cost of ink has been a barrier to adoption. Comparatively, the inks are more expensive than flexo or offset. However, he points out that with digital printing’s ability to batch print and manage the information flow it can be a catalyst to drive down converting costs in other areas of the value chain. “If you run that litho lam pet food tray on a coated white top sheet and double the sheet size off the C500 press versus running it on an offset press and an Asitrade, now you’re potentially diecutting a 20-out instead of a 10-out. That’s where a substantial reduction in converting costs come in, even with the increased cost of ink. If you are batching the printing and cutting of multiple SKUs, consider the setup efficiency and reduction of makeready waste versus litho or flexo; a dedicated value stream to specific graphic packaging applications becomes the de facto lowest cost method to make the box.”
Data Management Is Key Board converters might naturally question the efficiencies of coupling two machines together where a rotary diecutter becomes subordinate to a digital printer. Samotis says it is not about optimizing one routing step. It’s about optimizing a value stream and maximizing contribution dollars per hour
Converters also might debate the need to work in tandem with two OEMs when instead they could purchase a C500 press and run jobs on existing BW Papersystems or other OEM diecutters or even outsource the digitally printed sheets. Samotis says the collaboration between BWP and HP provide a high level of expertise, especially in the front-end processes, which are perhaps the biggest challenge for board converters when adopting digital printing.
HP and BW Papersystems are currently in conversation with customers interested in the new digital solution. The expectation is for an installation within the next 12 months.
“It is the information and data management that is so difficult,” he says. “To move from a discrete manufacturing process into a batch manufacturing process and to understand how you optimize that in the schedule, many box plants don’t have the necessary workflow tools and links to their MIS systems to effectively execute on a significant increase in transactions. There is also the decision making process on the front end in the design and the routing steps from a pre-press perspective for most efficient manufacturing in terms of how many outs and what board structure you run.”
The new digital collaboration will require a change in how each company individually deploys a machine into the corrugated industry. “When we’re doing an integrated project together on behalf of a customer, there will be members of BWP on what we call our Business Transformation Services (BTS) team,” Samotis says. “We will start the execution of BTS well ahead of install with the intent to provide an end-to-end solution that is ready to go upon completion of the value stream acceptance test. This integrated capability is the real value in the BWP/HP partnership that helps the customer transform from an analog world to a digital world.”
Both companies will be at ConneXion, the online community information channel launched by Brunton Business Publications, which goes live in November.
Original Article was Reprinted from from the November/December 2020 issue of Corrugated Today